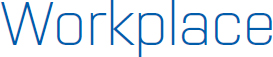
Workplace & Operating Practices
The health and safety of our employees underlies every aspect of how we operate, and is driven by policies, procedures, a culture of teamwork and efforts to continually improve how we conduct ourselves in our business at sea and onshore. Providing healthy work conditions, a safe environment and opportunities to advance and develop within the Company are critical to the well-being and fulfilment of our staff and the success of Pacific Basin.
KEY PERFORMANCE INDICATORS
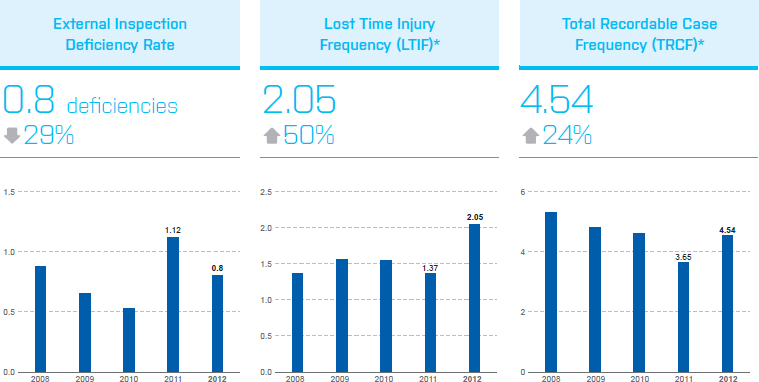
PERFORMANCE |
---|
Our average deficiencies per inspection reduced 29% to 0.8 and the frequency with which inspections found zero regulatory deficiencies was 75%. These results are among the best in the industry, especially considering our activity in the Far East where defects are typically raised in larger numbers and logged even if subsequently proven to be in order. Aim: To maintain our ships to a very high standard, a good measure of which is our performance in external Port State Control (PSC) inspections which we target to improve in 2013 through our policy of "zero defects in external checks through good self-checking" by "22 crew, 22 ownersTM". Regretfully the frequency of our "lost time injuries" increased 50% year on year, as such injuries increased from 12 in 2011 to 19 in 2012. Our total recordable case frequency increased 24% to 4.54. Our safety performance was impacted by increased slips, trips and falls. As part of our initiatives to rectify this record and for the benefit of the wider shipping industry, we cooperated with Videotel in the production of a film on ship safety. See page 49 for disclosure of two non work-related fatalities. Aim: To substantially eliminate our injury incidents and to better our best LTIF result of 0.85 in 2007. * LTIF is a principal measure of safety performance and is the number of lost time injuries (where the injured party misses at least 8 hours work) per man-hour worked multiplied by 1,000,000. TRCF measures the number of all recordable injuries per million man hours. |
HEALTH & SAFETY
We put safety first and publish clear policies and procedures for our ship and shore staff to follow. Our Performance Management System is a critical element in capturing performance and provides a mechanism for us to analyse failures when they do occur.
In 2012 there were two non work-related fatalities including one significant safety incident. One fatality occurred on board when a seaman died of natural causes. The other occurred when an off-duty seaman fell from a gangway. An investigation determined two causal factors: the gangway was not tightly rigged and the seaman tested positive for alcohol. Following the incident we circulated two safety bulletins to reinforce proper procedures in rigging a gangway and to alert staff that compliance with our drug and alcohol (D&A) policy is mandatory, violation of which could lead to suspension or termination of employment. Our D&A policy, along with other workplace and operational policies, are available on our website. We were deeply saddened by these losses and have extended our heartfelt condolences to the deceaseds' families.
High-performance teamwork at Pacific Basin is vital to our success. In addition to high crew standards, managers in our shore-based technical operations are former ships' Masters and Chief Engineers. This encourages a culture where problems are shared and where officers can rely on the very best, consistent support from ashore.
We promote concepts such as learning from Other People's Mistakes (OPM) and invest in non-standard measures to reduce risk such as the simple "3W" risk assessment prior to every task on board and the effective management of crew rest hours.
We encourage near-miss reporting which in 2012 accounted for 743 reports (2011: 675) through which officers and crew described safety incidents - however minor - that could have occurred and which were the basis for valuable advice to our seafarers on avoiding similar occurrences in the future.
Workplace safety, health and engagement metrics have been developed internally and follow best practices as defined by the industry and our peers. Shipping is a highly regulated industry and in all cases Pacific Basin meets all minimum requirements and in some cases exceeds requirements determined by local, regional and industry mandates and customer expectations.
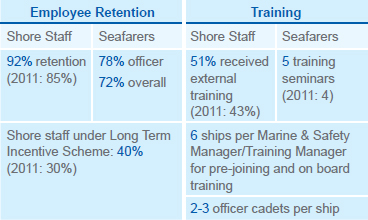
Our implementation of the Pacific Basin Management System ashore and at sea conforms to the mandatory International Safety Management (ISM) Code and a number of voluntary management standards as certified by Lloyd's Register Quality Assurance (LRQA), including:
- ISO 9001:2008
for our quality management system
- ISO 14001:2004
for our environmental management system
- OHSAS 18001:2007
for our occupational health & safety management system
Training & Development
Investment in the development and training of our staff at sea and ashore is key to maximising our crew and ship safety and productivity, and to motivating and retaining our people. This year we have introduced new metrics that capture training and staff retention for both seafarers and shore-based employees.
Communicating From Ship to Shore
In 2012 we deployed e-mail kiosks on all vessels in our owned and finance-leased fleet enabling seafarers the ability to anonymously report grievances or misconduct aboard. Reports must be made within 24 hours of an incident and all are investigated and appropriately handled. Generally the ship's Master assists with resolving matters that can be dealt with while at sea. Ten reports were received in 2012, none of which resulted in safety or environmental violations or disciplinary action.
ADDITIONAL WORKPLACE METRICS (as at 31 Dec 2012)
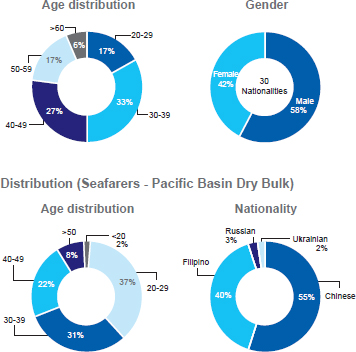